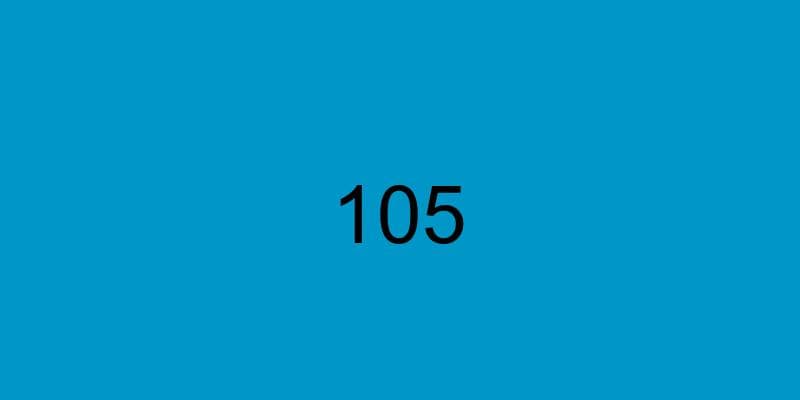
Polycarbonate (PC): Strength Under Pressure
In today’s world, not a
day goes by without using plastic products. Whether it’s your eyeglasses,
vehicle headlights or kitchen cookware, we are dependent on the strength of
engineered plastics like polycarbonate
(PC).
Among the many types of plastics, polycarbonate is renowned for its durability, lightweight and high impact resistance.
Let’s look at what makes PC so versatile.
The
history of PC
As early as the 1890s, German chemist Alfred Einhorn
experimented with reacting phosgene with bisphenol A (BPA). However, it wasn’t
until the mid-1950s that PC was commercially manufactured by Bayer and soon
after, other companies worldwide, including General Electric, began production.
As advancements in safety equipment, automotive, personal electronics and more
escalated, so did the use of PCs. However, environmental and health concerns
about BPA have grown, leading to increased research on ways to produce non-BPA
polycarbonates.
What
is PC material?
The ISO abbreviation for polycarbonate, PC, is a general term
for polymers with molecular chains called carbonate ester bonds. There are two
manufacturing methods:
1.
Phosgene
(solvent) method: Reacts bisphenol A (BPA) with phosgene
2.
Transesterification
(melt) method: Reacts bisphenol A (BPA) and diphenyl carbonate with phosgene
In short, BPA is dissolved into a sodium salt and then
mixed with a phosgene solution to create a reaction. From there, it is
separated from any impurities, rinsed, dried and turned into pellets.
PC density is higher than other common plastics, ranging from
1.20 to 1.22g/cm³.
Additives, like glass fibers and plasticizers, can have a significant impact on
not only the density of polycarbonate but also on polycarbonate yield strength.
Polycarbonate
processing and products
PC pellets
are easy to process into a wide range of products using a variety of methods,
like:
Injection Molding | Extrusion | Blow Molding | Thermoforming |
Car headlights & interior pieces | Bullet-resistant & shatterproof panels | Water bottles | Medical sterile packaging |
Consumer electronics | Signage & displays | Storage tanks | Point-of-sale displays |
Syringes & medical PPE | Tubes and piping (medical & construction) | Sporting protective gear | Electronics display panels |
Food containers | Roofing | Toys & play equipment | Furniture components |
Sports equipment & outdoor gear | Decorative construction elements | Containers (medical & food) | Industrial control panels |
Lighting | Insulation | Automotive air ducts | Skylights |
Eyeglasses | Industrial protective covering | Pressure vessels | Aircraft, bus and train interiors |
Polycarbonate texture varies from smooth and glossy to matte,
textured, frosted or rough, depending on the processing method chosen. The surface finish of a polycarbonate mold is critical to PCs final texture and look. But no
matter how much you use it, PC won't break easily and it has great design
potential.
What
are the features of PC?
·
Resilience: Polycarbonate chemical
resistance includes water, alcohols, organic and inorganic acids and alkalis
·
Durability: Withstand wear, pressure and damage
over long periods, even in low temperatures between -30℃ and -40℃
·
Polycarbonate
impact resistance:
Tolerates force without breaking, cracking or deforming
·
Transparency: At a thickness of
2mm to 3mm, the light transmittance is 85% to 90%, which is roughly equivalent
to that of methacrylic resin
·
Heat resistance: Stable mechanical properties between -40℃ to 120℃
·
Dimensional
stability: There is little change when exposed
to high heats or with water absorption
·
Food hygiene: Minimal
leaching makes it compliant with food hygiene standards (Notification No. 20)
Despite PC being one of the most widely used general-purpose
engineering plastics, there are some drawbacks. Polycarbonate’s thermal
conductivity is low compared to other materials, it is
costly, may become brittle with exposure to UV radiation and is open to easy
abrasion. Scratch resistant polycarbonate is available, but coatings or treatments must
be applied.
Polycarbonate
FAQs
Q: Does polycarbonate block UV?
A: PC give some
level of UV resistance, but prolonged exposure to UV radiation may result in
yellowing, loss of mechanical properties and brittleness.
Q: Is polycarbonate recyclable?
A: Yes, though there are several steps to guarantee it is
ready for new products.
Q: Is polycarbonate strong?
A: Yes, it is known for its durability
and is one of the strongest thermoplastics produced.
Q: Can you laser cut polycarbonate?
A: It is possible, but there are safety
concerns along with the consideration of material thickness, possible melting
and discoloration and laser settings.
Q: What is the melting point of
polycarbonate?
A: PC has a fairly high melting point of
267°C or 512°F